A fully automated corn chips production line that includes three filling and wrapping machines and a weighing system with a production capacity of 200 kg.
π½ Automatic Corn Chips Production Line β Clean, Hand-Free Production This line is used to produce corn chips (puffs or snacks) completely without any manual intervention. The process begins with mixing the corn flour, then shaping it inside an extruder. It is then dried, flavored, and automatically packaged into bags. β The line operates fully automatically β from the beginning of production to packaging. β Complete hygiene and high quality β no human contact is required during production. β Designed according to global health standards β ideal for modern factories. β Easy and fast production β with just the push of a button, operation begins.
The line consists of the following parts
1_corn mixer 2_The spiral conveyor 3_Extruder 4_Conveyor belt for the product 5_ Grill oven on hot air 6_Flavor mixing tanks 7_Flavor pump 8_The spiced flavoring cylinder 9_A line that becomes a server for packing machines 10_Packing and wrapping machines
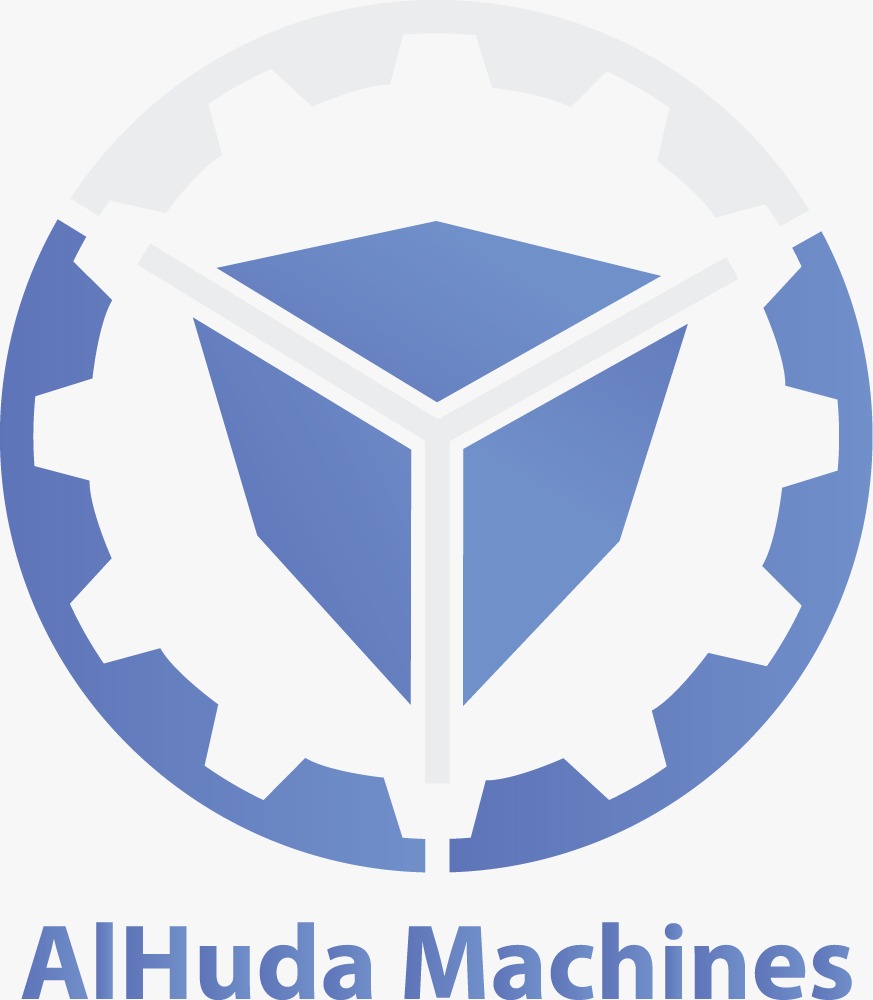
Corn mixer
Homogeneous and precise mixing of corn to the highest quality standards. The corn mixer is essential equipment for preparing corn before the manufacturing stages. It achieves perfect homogeneity in the corn mixture by adding a precise percentage of moisture, ensuring even distribution and professional preparation of the final product. Advanced Operation Mechanism 1οΈβ£ Large Capacity and High-Quality Materials Capacity: 400 kg, allowing for efficient processing of large quantities of corn. Material: Made entirely of 2 mm thick food-grade 304 stainless steel, ensuring rust resistance and maintaining product hygiene. 2οΈβ£ Powerful Motor to Ensure Perfect Mixing Main Motor: 5 HP, Turkish-made, ensuring stable performance and high mixing efficiency. A homogeneous mixing mechanism ensures perfect distribution of ingredients inside the mixer. 3οΈβ£ Precise Corn Moisture Control Equipped with a built-in water tank that allows for precise control of the corn moisture level to achieve the desired consistency. A water level indicator helps accurately adjust the quantity during the mixing process. 4οΈβ£ High-security worker protection system Equipped with mechanical protection (metal mesh) that prevents workers from entering the mixer during operation, ensuring a safe working environment. 5οΈβ£ Smooth unloading and process control system Equipped with a standard unloading port that allows easy product removal without clumping or loss of raw materials. Equipped with a monitoring and cleaning port, allowing for monitoring the mixing process and ensuring the cleanliness of the mixer after each use. 6οΈβ£ Effective removal of metal impurities The mixer basin contains a powerful magnet that removes any metal impurities from the corn, ensuring the purity of the final product and preventing unwanted materials from entering subsequent production lines. Technical Specifications β Material: Made entirely of food-grade 304 stainless steel to ensure the highest standards of hygiene and quality. β Electrical Power: 3.75 kW | 380/220 V | 50 Hz. β Dimensions: Length: 180 cm Width: 120 cm Height: 230 cm β Machine Number: 001 β Model: THV-2025PV-Z β Country of Manufacture: Turkey β High-quality industrial materials according to European standards. Durable construction and highly efficient performance βοΈ 2 mm thick interior design for corrosion resistance and long-lasting durability. βοΈ Smooth discharge system allows for easy control of the corn extraction process after mixing. βοΈ High mechanical protection to ensure worker safety during operation. βοΈ Magnets inside the tub to remove any metal impurities that may affect product quality. βοΈ Precise control of corn moisture through a built-in water tank and level indicator. βοΈ Robust and durable design made entirely of food-grade 304 stainless steel to ensure maximum hygiene. βοΈ High-security system with a metal mesh to prevent hand entry during operation. βοΈ Effective removal of metal impurities using the built-in tub magnet. βοΈ Easy emptying and cleaning via dedicated openings. βοΈ High-performance motor to ensure optimal mixing efficiency and highest quality. π‘ The ideal solution to ensure homogeneous mixing and professional corn preparation with the best quality and operational efficiency!
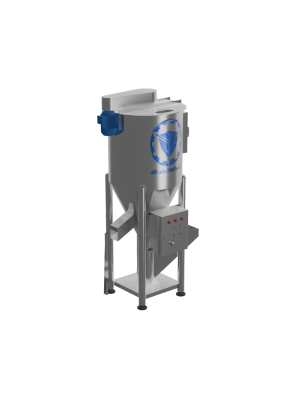
Screw conveyor
Precise, Efficient, and Safe Automated Material Transfer The spiral conveyor is one of the most important pieces of equipment in production lines. It automatically feeds materials into the extruder in a smooth and efficient manner, ensuring a consistent flow and improving production efficiency with the highest levels of safety and quality. Advanced Operation Mechanism 1οΈβ£ Spacious tank made of high-quality materials Capacity: 75 kg, allowing sufficient storage of materials to ensure continuous production without interruption. Material: Made entirely of 2 mm thick food-grade 304 stainless steel, providing high rust resistance and ensuring product hygiene. 2οΈβ£ Automatic extruder feeding to ensure consistent flow The conveyor automatically feeds materials into the extruder, reducing the need for manual intervention and ensuring efficient work continuity. A precise spiral design ensures smooth material transfer without clumping or interrupting flow. 3οΈβ£ High-security worker protection system Equipped with a metal mesh as mechanical protection to prevent the worker's hand from entering the conveyor during operation, providing a safe working environment. 4οΈβ£ Efficient Metal Impurities Removal Equipped with an advanced magnetic mechanism that removes any metal impurities that may be present within the materials, preserving the quality of the final product and protecting the machines from damage. 5οΈβ£ Ease of Cleaning and Maintenance Equipped with a dedicated bottom opening for cleaning, facilitating periodic maintenance and removing any material residue inside the tank. Technical Specifications β Material: Made entirely of 304 food-grade stainless steel to ensure the highest standards of hygiene and quality. β Electrical Power: 1.25 kW | 380/220 V | 50 Hz. β Dimensions: Length: 300 cm Width: 90 cm Height: 250 cm β Machine Number: 002 β Model: THV-2025PV-Z β Country of Origin: Turkey β High industrial quality according to European standards. β Robust design and high operating efficiency β 2 mm thick internal structure for corrosion resistance and long-lasting durability. βοΈ Precise spiral design for uniform material transfer without clumping. βοΈ Easy discharge system via the bottom opening, facilitating maintenance and cleaning. βοΈ High mechanical protection to ensure worker safety during operation. βοΈ Efficient removal of metal impurities using the built-in magnet. βοΈ Automatic extruder feeding to ensure consistent flow and improve production efficiency. βοΈ Durable construction made of food-grade 304 stainless steel to maintain hygiene and quality. βοΈ Integrated safety system with metal mesh to prevent accidents during operation. βοΈ Efficient removal of metal impurities using a built-in magnetic system. βοΈ Easy maintenance and cleaning thanks to the dedicated bottom opening. βοΈ Energy-saving design with low electricity consumption. π‘ The ideal solution for precise and safe material transfer, while achieving the highest standards of quality and operational efficiency!
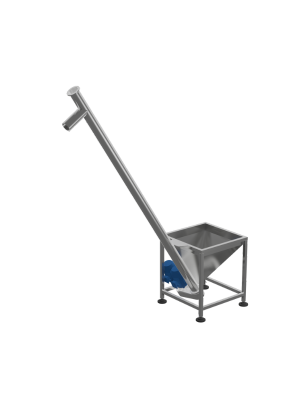
Extruder
Professional Performance for the Production of the Highest-Quality Puffed Grains The extruder is an essential piece of equipment in the food industry. It produces puffed grains in various shapes using advanced manufacturing techniques, ensuring consistent production with high efficiency and precise control over the shape and size of the final product. Advanced Operation Mechanism 1οΈβ£ High Production Capacity and Continuous Operational Efficiency Production capacity: Ranges from 200 kg per hour, depending on the desired grain shape. Designed for 24-hour continuous operation thanks to a heavy-duty gearbox made from the finest metals according to American Extrusion standards. 2οΈβ£ Robust Structure to Ensure Durability and Sustainability The main carrier is made of steel heat-coated using the latest furnaces to protect it from corrosion and shocks. Fully insulated with a layer of food-grade 304 stainless steel to ensure easy cleaning and adherence to health standards. Approximate Weight: 1300 kg, providing stability and consistency during operation. 3οΈβ£ Advanced transmission system for higher reliability. The bearings and bearings are Swedish and Japanese-made SKF, ensuring smooth performance and a long operational life. The screws are made of the finest metals and heat-treated using the latest vacuum furnace technology, ensuring they can withstand high temperatures and pressures during operation. Equipped with a main screw that automatically feeds material to the compressor screw via an inverter, allowing precise control of the feeding process. 4οΈβ£ Integrated electronic control for flexible operation. All extruder motors are electronically controlled via three inverters, ensuring smooth control at various speeds. An electronically variable speed inverter knife allows for easy adjustment of the grain length according to production needs. Equipped with a start-up heater with precise electronic temperature control. 5οΈβ£ Dual cooling to maintain stable performance. A closed-circuit water-cooled system based on the American Extrusion model ensures high cooling efficiency and reduces water consumption. An additional air-cooled system maintains stable temperatures during continuous operation. 6οΈβ£ Smart control panel for efficient process monitoring An independent main control panel made of food-grade 304 stainless steel, equipped with a special ventilation system for hot areas. Equipped with 3 ventilation filters and 3 cooling fans to ensure stable performance in harsh industrial environments. The control panel is tightly insulated to prevent dust ingress, ensuring clean and stable operation. Equipped with a classic panel for full control of the operating mechanism, along with an advanced software system capable of automatically reading faults and alerting in the event of any malfunction. The ability to automatically store operating data, with a detailed electrical diagram included for easy maintenance and inspection. Technical Specifications β Material: Made entirely of food-grade 304 stainless steel to ensure the highest standards of quality and hygiene. β Electrical Power: 45 kW | 380/220 V | 50 Hz. β Dimensions: Length: 150 cm Width: 110 cm Height: 240 cm β Machine Number: 003 β Model: THV-2025PV-Z β Country of Manufacture: Turkey - High industrial quality according to European standards. Durable Design and Highly Efficient Performance βοΈ Main stand made of heat-treated steel to withstand harsh operating conditions. βοΈ Automatic feeding system via an electronically controlled main screw to ensure a consistent flow of material. βοΈ 50 HP (37 kW) Italian-made screw compressor motor with copper windings for durability and stable performance. βοΈ Main motor body made of cast iron for increased durability and pressure tolerance. βοΈ Fully electronic speed and length control via advanced inverter devices. βοΈ Dual cooling system (water + air) to maintain constant temperatures during continuous operation. βοΈ Smart, tightly insulated control panel with a special cooling and ventilation system for hot areas. βοΈ Production capacity up to 200 kg/hour with easy grain shape control. βοΈ Powerful, highly efficient motors from trusted international brands to ensure hygiene and easy cleaning. βοΈ Durable, food-grade 304 stainless steel design ensures cleanliness and ease of cleaning. βοΈ Dual cooling system maintains stable performance and prevents overheating. βοΈ Fully electronically controlled by advanced inverters to ensure precise and smooth operation. βοΈ Advanced control panel capable of reading faults and storing operational data. βοΈ Safe and environmentally friendly design with a closed cooling system to save water. π‘ The ideal solution for producing high-quality puffed grains, with the highest levels of efficiency and consistent performance!
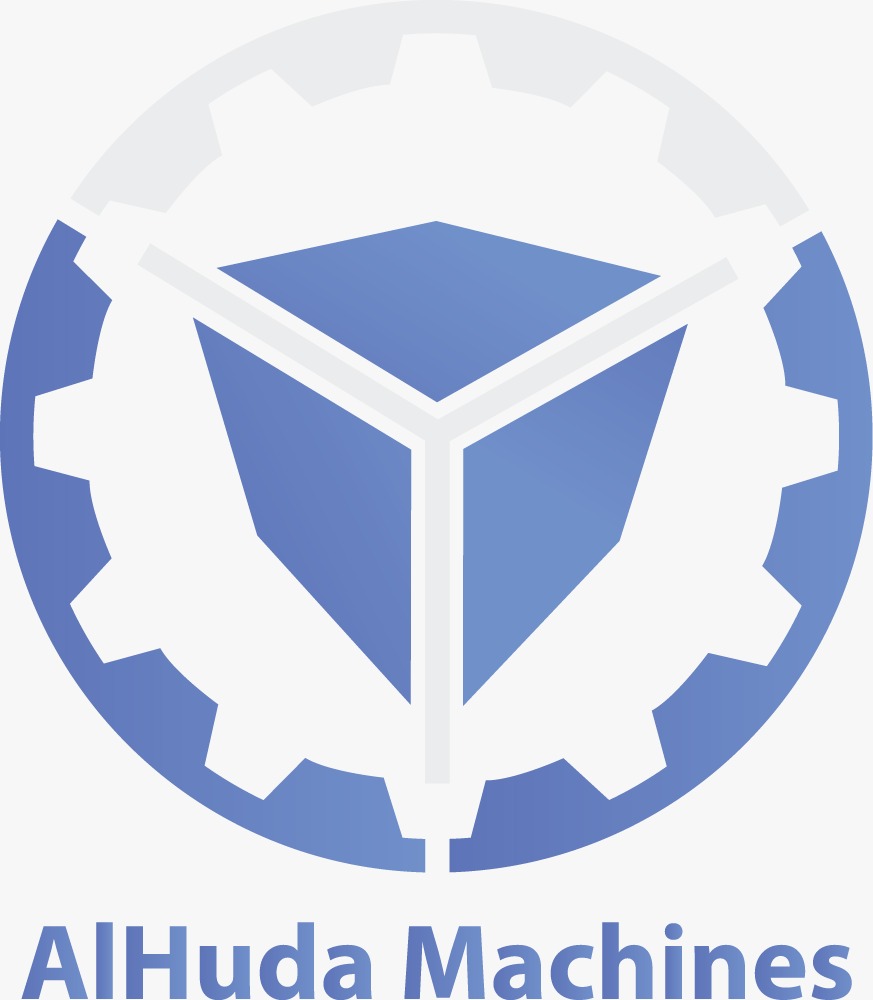
Conveyor belt for the product
Professional Product Transfer Between Manufacturing Stages Conveyor belts are essential equipment in production lines. They ensure smooth and safe transfer of materials from the extruder to the oven, thanks to their robust design and advanced features that guarantee the highest standards of hygiene and efficiency. Advanced Operation Mechanism 1οΈβ£ Sturdy structure to ensure durability and sustainability Made entirely of 304 food-grade stainless steel, ensuring high rust resistance and easy cleaning. Equipped with sturdy wheels to facilitate movement and periodic cleaning within the production line. 2οΈβ£ High-quality food-grade conveyor belt The conveyor belt is made of PVC or food-grade plastic to ensure hygienic and safe product transfer. The surface has a non-stick texture to prevent material from sticking during transport, thus preserving product quality. 3οΈβ£ Integrated Cleaning System Equipped with dedicated cleaning slots to facilitate periodic maintenance and prevent residue buildup. It includes automated cleaning brushes that operate continuously to remove any impurities or residual materials during operation. 4οΈβ£ Economical Operation with High Efficiency Low power consumption (1.25 kW), ensuring economical operation without energy waste. Technical Specifications β Material: Made entirely of food-grade 304 stainless steel to ensure hygiene and durability. β Electrical Power: 1.25 kW | 380/220 V | 50 Hz. β Dimensions: Length: 300 cm Width: 80 cm Height: 200 cm β Machine Number: 004 β Model: THV-2025PV-Z β Country of Manufacture: Turkey β High industrial quality according to European standards. Product Conveyor Features βοΈ Durable design entirely made of food-grade 304 stainless steel to ensure the highest hygiene standards. βοΈ Smooth and safe transfer of materials from the extruder to the oven without any damage to the product. βοΈ Conveyor belt made of PVC or food-grade plastic to ensure hygienic transportation. βοΈ Integrated automated cleaning system with cleaning brushes and maintenance ports. βοΈ Wheels for easy movement and cleaning, providing operational flexibility. βοΈ Low energy consumption with high operating efficiency. π‘ The ideal solution for safely and efficiently transporting product within food production lines!
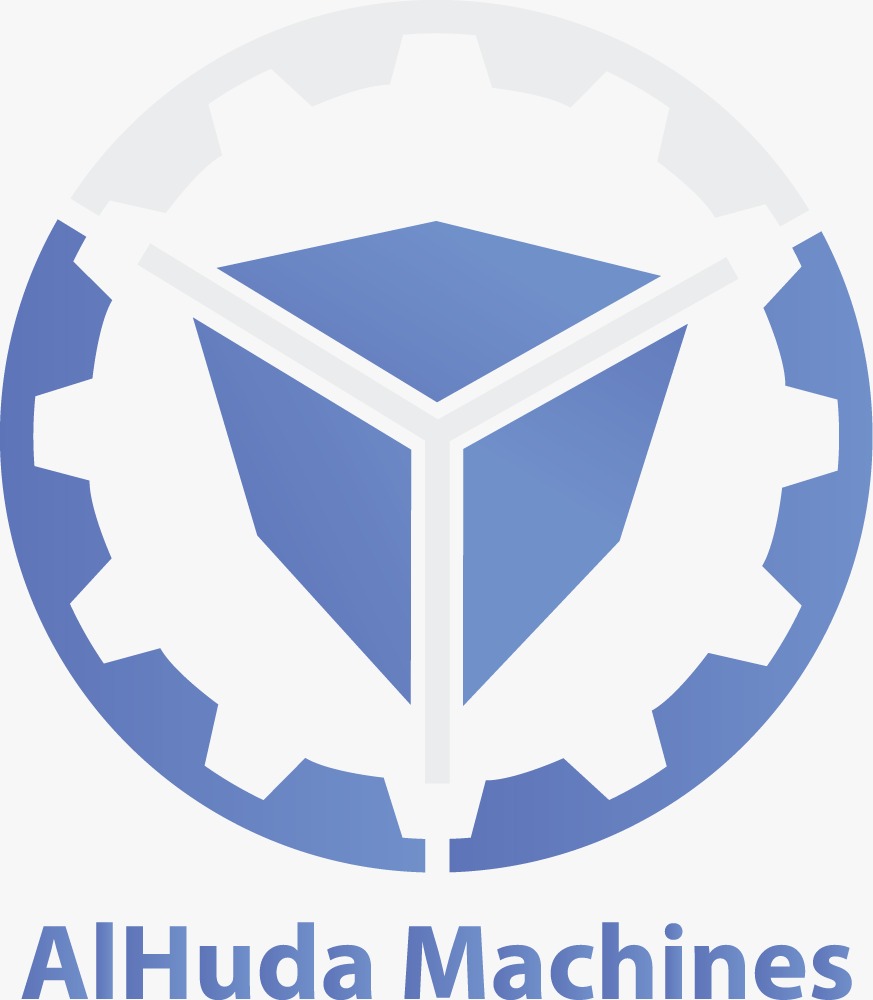
Hot air grill oven
Professional Roasting and Drying Using Hot Air Technology The hot air roasting oven is one of the latest technologies used in roasting and drying chips. It relies on homogeneous heat distribution to ensure the production of a final product of optimal quality, with precise humidity and temperature control to adjust the texture and taste as desired. Advanced Operation Mechanism 1οΈβ£ High productivity with precise temperature control Production capacity up to 300 kg per hour, making it ideal for large production lines. The temperature can be adjusted up to 300Β°C depending on the product type and manufacturing requirements. The humidity of the final product can be controlled from 0% to 5% as required to ensure the ideal texture. 2οΈβ£ Efficient and Energy-Saving Heating System Operates on diesel or natural gas (LPG) as desired by the customer, ensuring economical and efficient operation. Equipped with a built-in heating chamber that can be detached and installed for easy maintenance. Made of 304 chrome and stainless steel, it can withstand temperatures up to 800Β°C. The primary burner is Baltur or Riello (Italian - Model 2025), ensuring high operating efficiency. 3οΈβ£ Robust construction and perfect thermal insulation Made entirely of 304 food-grade stainless steel to ensure high rust resistance and ease of cleaning. The oven is fully insulated with a 15 cm thick fiberglass layer on all sides to maintain internal heat and reduce energy consumption. 4οΈβ£ Advanced product conveyor system with automatic cleaning The conveyor belt is made of 100 cm wide 304 food-grade stainless steel, ensuring even roasting. It is equipped with an automatic conveyor belt cleaning mechanism, maintaining product cleanliness and operating efficiency. The oven is equipped with an LS inverter for precise control of the conveyor belt speed. 5οΈβ£ Professional air distribution for homogeneous roasting Equipped with powerful hot air pumping and circulating fans to ensure optimal heat distribution from the top and bottom with side recirculation. 3 HP hot air pumping fan motor (Italian or Turkish - excellent quality). 3 HP air extraction and circulation fan motor (Italian or Turkish - excellent quality). 6οΈβ£ Advanced operating and control system A separate control panel made of food-grade 304 stainless steel, removable and retractable for easy maintenance and transportation. A modern touch screen control panel equipped with a smart fault reading system via text messages to quickly identify and resolve problems. All electrical parts are Schneider, France, and LS, Korea, to ensure high operational reliability. The main gearbox is Italian, and the motors are Italian or Turkish, of excellent quality. The rotation of the hot air extraction and circulation fans is electronically controlled via inverters. Technical Specifications β Material: Made entirely of food-grade 304 stainless steel to ensure the highest standards of hygiene and quality. β Electrical Power: 10.5 kW | 380/220 V | 50 Hz. β Dimensions: Length: 650 cm Width: 140 cm Height: 200 cm β Machine Number: 005 β Model: THV-2025PV-Z β Country of Manufacture: Turkey - High industrial quality according to European standards. Features of the Hot Air Roasting Oven βοΈ High production capacity of up to 300 kg/hour with precise humidity and temperature control. βοΈ Durable design and optimal thermal insulation to maintain internal temperature and reduce energy consumption. βοΈ Integrated heating chamber that can be disassembled and installed for easy maintenance. βοΈ Advanced air distribution system to ensure even roasting on all sides. βοΈ Conveyor grill made of 304 food-grade stainless steel with an automatic cleaning system. βοΈ Smart touch screen control panel with automatic fault reading system. βοΈ Powerful European-quality motors and fans to ensure continuous production. π‘ The perfect solution for high-quality roasted chips, delicious taste, and perfect texture!
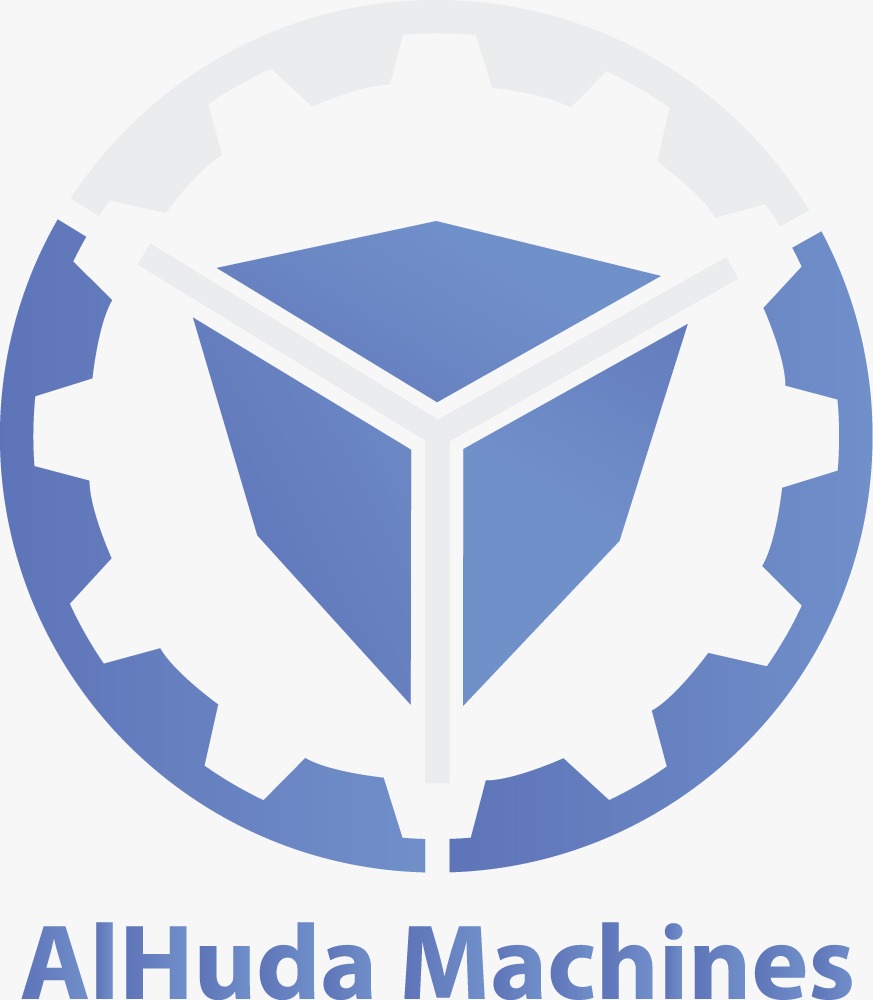
Two flavor mixer tanks
Precise Flavor Preparation with Indirect Heating Technology The flavor cooking tanks are designed to ensure the highest quality food flavors are prepared. They rely on an indirect heating system (double jacket) to provide even heating without affecting the flavor composition, enhancing optimal flavor distribution throughout the final product. Advanced Operation Mechanism 1οΈβ£ Professionally Designed Indirect Heating System The tank is manufactured using double jacket technology, which allows the surrounding water to be heated instead of directly heating the flavor. This ensures that the flavor is maintained at its optimal quality without burning or changing its composition. It has a heating capacity of approximately 200 liters, making it ideal for large production lines. It is equipped with an indicator to monitor the hot water level inside the tank to ensure proper and continuous operation. 2οΈβ£ Durable and Industrial-Resistant Construction Made entirely of food-grade 304 stainless steel, ensuring high rust resistance and ease of cleaning and sterilization. The main chassis is made of heat-coated steel and covered with stainless steel to ensure high durability and added protection. The tanks and pump are mounted on a single chassis for easy installation and maintenance. It is equipped with sturdy wheels for easy movement and cleaning, making it easy to move within production lines. 3οΈβ£ Precise Temperature Control System Equipped with a digital thermometer to continuously read the temperature of the hot water inside the tank, ensuring precise control of the heating process. A homogeneous heat distribution system prevents the formation of heat spots within the flavor, ensuring a consistent final product. Technical Specifications β Material: Made entirely of food-grade 304 stainless steel to ensure the highest standards of hygiene and quality. β Electrical Power: 3.75 kW | 380/220 V | 50 Hz. β Dimensions: Length: 230 cm Width: 130 cm Height: 170 cm β Machine Number: 006 β Model: THV-2025PV-Z β Country of Manufacture: Turkey - High industrial quality according to European standards. Flavor Cooking Tank Features βοΈ Double jacket design for indirect heating, preserving flavor quality. βοΈ Made entirely of food-grade 304 stainless steel for rust resistance and easy cleaning. βοΈ Equipped with a hot water level indicator and a thermometer for precise temperature monitoring. βοΈ Sturdy chassis made of heat-coated steel for durability and longevity. βοΈ Equipped with wheels for easy movement and cleaning, making it easy to use on various production lines. βοΈ Large capacity of up to 250 liters, making it ideal for mass industrial production. π‘ The perfect solution for preparing flavors with the highest levels of precision and quality!
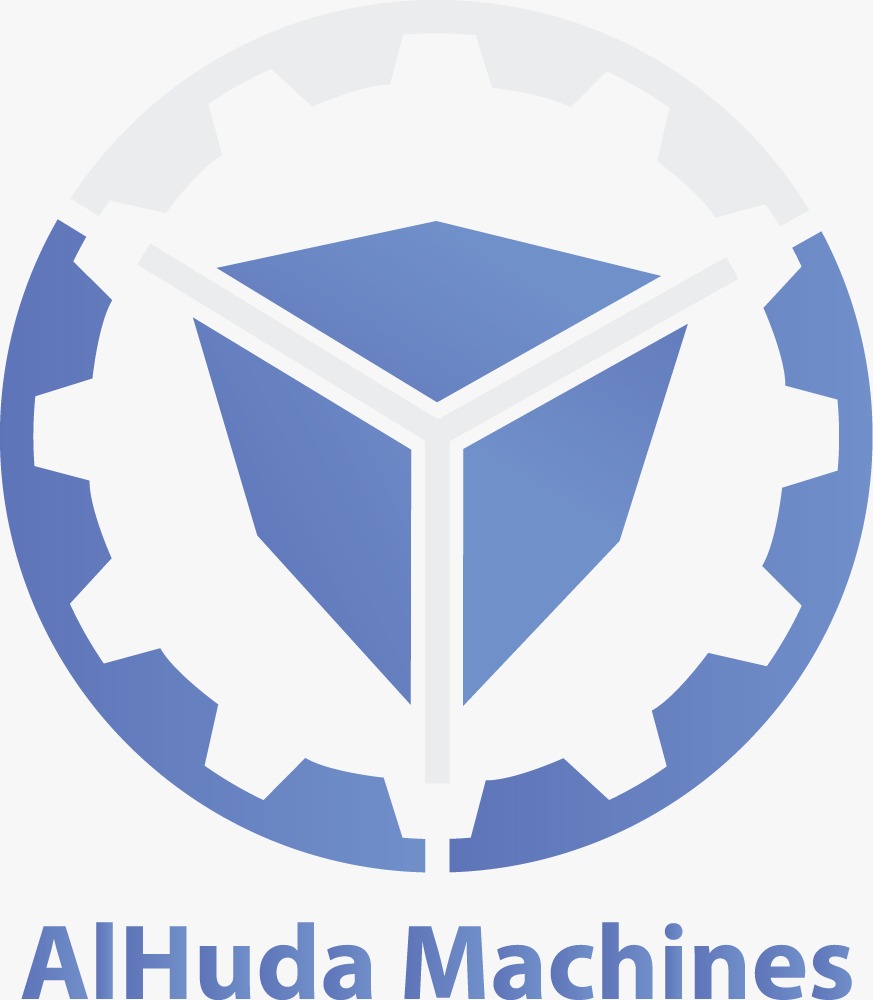
Flavor pump
Advanced Technology for Precise and Efficient Flavor Delivery The flavor pump is one of the most important components of the chips production line. It pumps and distributes flavor with extreme precision through an alternating suction and pumping system, helping to conserve flavor consumption and ensure consistent coverage of the final product. Advanced Operation Mechanism 1οΈβ£ Alternating Suction and Pumping Technology (Advanced American System) The pump relies on an alternating suction and pumping system, a modern American technology that precisely adjusts flavor flow and reduces waste, resulting in economical flavor consumption with the highest efficiency. 2οΈβ£ Powerful Motor and Robust Construction Equipped with a durable, high-quality, European-made aluminum pump, ensuring reliable performance and consistent pumping speed. The pump body is made of solid European aluminum, making it corrosion-resistant and capable of withstanding continuous operation. 3οΈβ£ Precise Electronic Control of Flavor Quantity The flavor quantity is electronically controlled via an inverter, allowing the pumping rate to be adjusted according to the product type and production needs. 4οΈβ£ Practical and Easy-to-Maintain Design The pump is mounted on a support platform made of food-grade 304 stainless steel, providing stability and ease of movement and cleaning. The connection between the motor and pump is via a flexible rubber coupling, facilitating quick maintenance and disassembly. It is equipped with a Spanish-made food-grade silicone hose, ensuring safe flavor transfer without compromising quality. The body is equipped with sturdy wheels for easy movement and cleaning, making it ideal for use in industrial production lines. Technical Specifications β Material: Made entirely of food-grade 304 stainless steel to ensure the highest levels of hygiene and quality. β Electrical Power: 1.125 kW | 380/220 V | 50 Hz. β Dimensions: Length: 80 cm Width: 60 cm Height: 80 cm β Machine Number: 008 β Model: THV-2025PV-Z β Country of Origin: Turkey - High-quality manufacturing according to European standards. βοΈ Advanced American technology to control flavor flow and reduce waste. βοΈ Powerful Encarnage motor and European-made aluminum pump for consistent performance. βοΈ Precise electronic inverter control of flavor injection quantity. βοΈ Practical design with a 304 food-grade stainless steel platform equipped with wheels. βοΈ Easy maintenance thanks to a rubber coupling for easy assembly and removal. βοΈ Equipped with a Spanish food-grade silicone hose for safe flavor transfer. π‘ The perfect solution for efficient flavor injection and ensuring a consistent taste in every chip!
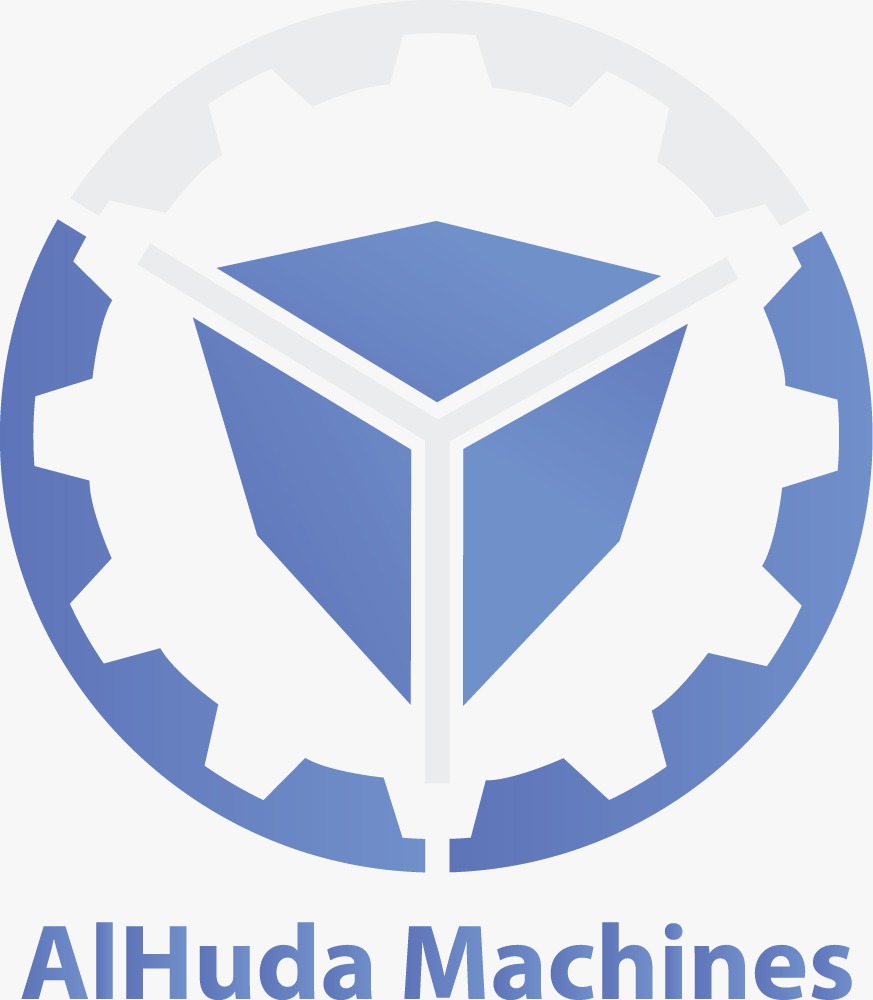
Flavor coating cylinder
Homogeneous Flavoring for the Best Taste and Quality The seasoning is one of the most important stages in chip production. It ensures even flavor distribution across all chips using an advanced flavor spray system and a slow, balanced rotation mechanism that prevents clumping or settling. Advanced Mechanism 1οΈβ£ Precise Electronic Control System The rotation speed of the seasoning is electronically controlled via an inverter, allowing the time the chips pass through the drum to be adjusted according to the product type. The seasoning is calibrated to adjust the flavor level as needed, ensuring consistent results for each batch. 2οΈβ£ Advanced Flavor Spray for Optimal Coverage Equipped with a high-precision flavor spray (an advanced calibrated American model), ensuring even and precise flavor distribution without waste. The scales inside the drum are designed to prevent flavor clumping, helping achieve even flavoring for each chip. 3οΈβ£ Impurity ejection mechanism and improved product quality Equipped with an automatic ejection mechanism for unwanted impurities and small particles, ensuring the final product has the perfect size and texture. The chips rotate slowly while dispersing the flavor, helping to fully coat the chips without breaking them. 4οΈβ£ Durable and Easy-to-Clean Design Made entirely of 304 food-grade stainless steel to ensure the highest standards of hygiene and health. Equipped with a chrome cover at the material exit end to protect the product and prevent waste. Equipped with sturdy wheels for easy movement and cleaning, making it ideal for industrial environments. Technical Specifications β Material: Made entirely of 304 food-grade stainless steel to ensure the highest levels of hygiene and quality. β Electrical Power: 3.75 kW | 380/220 V | 50 Hz. β Dimensions: Length: 300 cm Width: 120 cm Height: 150 cm β Machine Number: 007 β Model: THV-2025PV-Z β Country of Origin: Turkey - High industrial quality according to European standards. Marinator Features βοΈ Electronic inverter control system to adjust the drum rotation speed. βοΈ Advanced American flavor sprayer for optimal flavor distribution. βοΈ Internal design with scales to prevent flavor clumping and ensure consistent flavoring. βοΈ Automatic ejection mechanism for unwanted impurities and particles. βοΈ Made entirely of 304 food-grade stainless steel for rust resistance and easy cleaning. βοΈ Equipped with sturdy wheels for easy stirring and cleaning. π‘ The perfect solution for consistent flavoring and ensuring high-quality chips!
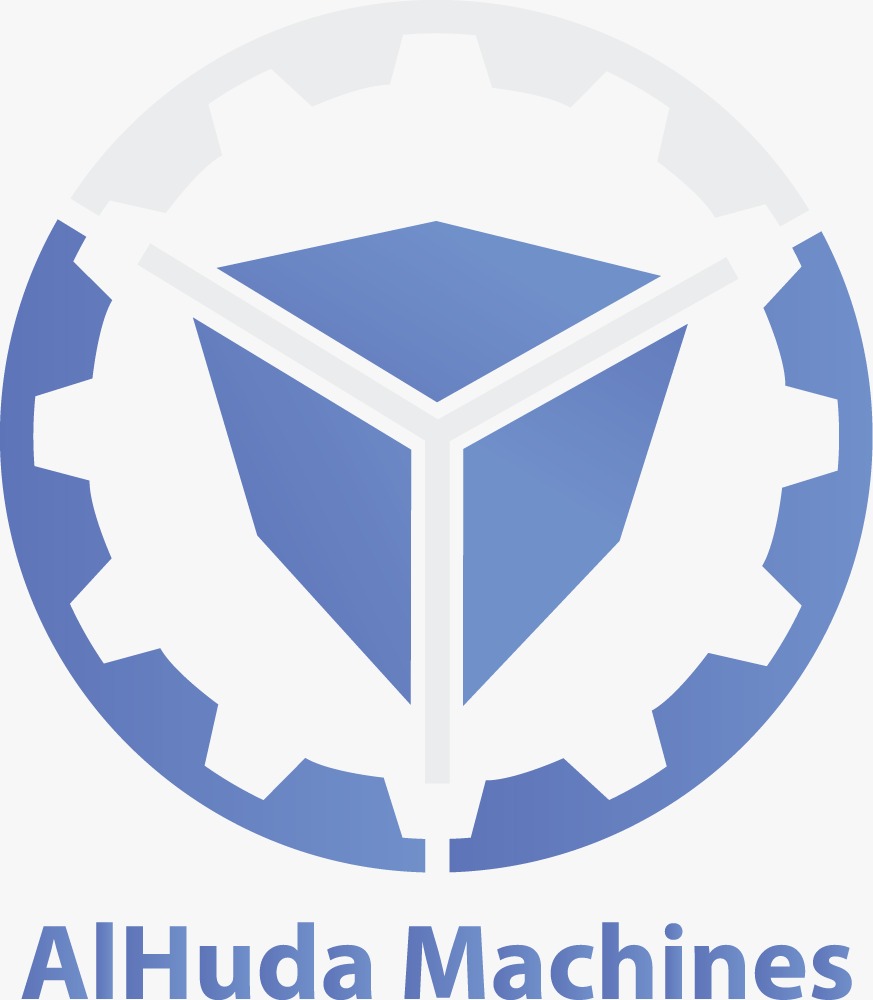
Server conveyor belt
Precise and Balanced Conveyance to Maintain Product Quality The conveyor belt is one of the most important stages of potato chips production. It ensures efficient transfer of the product from the flavoring stage to three packaging machines, while preserving the integrity of the chips through a fully automated and precise distribution system. Advanced Operation Mechanism 1οΈβ£ Precise Electronic Control System The product transfer speed is controlled by an electronic control circuit equipped with modern sensors, allowing for balanced product feeding according to the capacity of the packaging machines. β Equipped with a reservoir and vibrator to ensure a homogeneous flow of chips without accumulation or jamming. β Fully automated to reduce manual intervention and increase production efficiency. 2οΈβ£ Conveyor belt with an advanced design equipped with a Z-shaped PVC belt to facilitate product transfer at an appropriate angle, helping achieve optimal flow without affecting the shape of the chips. β Made of food-grade 304 stainless steel to ensure the highest standards of hygiene and quality. β Its design reduces vibration and shock, keeping the product unbroken. 3οΈβ£ Smart Sensors for Improved Performance It features advanced electronic sensors that automatically adjust the speed and flow of the product, preventing any buildup or congestion in the production line. β Ensures even product distribution between the packaging machines for stable and consistent production. 4οΈβ£ Durable and Easy-to-Clean Design Made entirely of food-grade 304 stainless steel to ensure rust resistance and easy cleaning, with a robust structure to withstand continuous operation in industrial environments. β Equipped with sturdy wheels for easy movement and maintenance. Technical Specifications β Material: Made entirely of food-grade 304 stainless steel to ensure the highest levels of hygiene and quality. β Electrical Power: 5.25 kW | 380/220 V | 50 Hz. β Dimensions: Length: 14 cm Width: 90 cm Height: 380 cm β Machine Number: 009 β Model: THV-2025PV-Z β Country of Manufacture: Turkey Features of the Feeding Conveyor Line βοΈ Precise electronic control system with sensors to automatically adjust the product conveying speed. βοΈ Z-shaped PVC conveyor ensures optimal flow without compromising the quality of the slices. βοΈ Shock and vibration-resistant design to protect the product from breakage. βοΈ Tank and vibrator to ensure consistent flow and prevent product accumulation during conveying. βοΈ Made entirely of food-grade 304 stainless steel for rust resistance and easy cleaning. βοΈ Equipped with sturdy wheels for easy movement and cleaning, making it ideal for industrial environments. π‘ The ideal solution for efficient product transfer and ensuring the highest levels of production quality!

CONTINUOUS SYSTEM GRAVIMETRIC PACKAGING MACHINES 3PCS
Accurate and Speedy Food Packaging with Advanced Systems The weight packaging machine is designed according to the latest international technologies to ensure high speed, 24-hour operation, and superior accuracy in weighing and packaging. It features advanced drive systems, precise optical sensors, and an integrated electronic control system that ensures high efficiency and consistent production. Advanced Operation Mechanism: 1οΈβ£ Precise and Flexible Packaging System Automatic packaging of potato chips, chips, seeds, and nuts. Relies on an intelligent weighing system to ensure accurate packaging and reduce waste. 2οΈβ£ Advanced Electronic Control for Smooth Operations Advanced PLC system from Delta for fast response and precise control. 7-inch electronic touch screen from Delta for ease of operation. Precise OMRON thermal control system allows temperature adjustment from the screen to ensure weld quality. 3οΈβ£ High Performance with Powerful Motors Equipped with motors and gearboxes to control the conveyor belt and jaws, ensuring stable operation. A stepper motor for automatic roll holder movement, controlled via a screen. A stepper motor for roll drawback compensation, with an alarm system when the roll is finished. 4οΈβ£ Safe and durable design Safety sensors protect the operator from any operational errors. A comprehensive daily production counter for performance monitoring and effective production tracking. The entire body is made of 304 food-grade stainless steel to ensure hygiene and product safety. All parts in contact with the product are made of 304 stainless steel in accordance with food-grade quality standards. 5οΈβ£ Flexible roll usage Roll width can be customized to suit customer requirements, allowing for the packaging of a variety of products. Maximum roll length: 320 mm. An Italian-made roll forming device, easy to replace for increased operational efficiency. Supports the use of built-in cellophane rolls to ensure tight, high-quality packaging. 6οΈβ£ Additional equipment for increased efficiency A Z-type PVC conveyor belt with a 304 stainless steel body and an automatic feeding system. Conveyor belt for finished packages to ensure easy transportation and storage. Date printer to print product information directly onto the package. Smart weighing system from HIGH DREAM to ensure high weight accuracy. Weighing platform made of 304 stainless steel to ensure stability and reliability. Technical Specifications: β Material: Made entirely of food-grade 304 stainless steel to maintain hygiene and quality. β Electrical Power: 5.75 kW | 380/220 V | 50 Hz. β Dimensions: Length: 200 cm Width: 130 cm Height: 420 cm π’ Machine Number: 024 β Model: THV-2024PV-B β Country of Origin: Turkey Durable design to ensure high performance: βοΈ High weight accuracy via the intelligent summation system. βοΈ Comprehensive electronic control for maximum operational efficiency. βοΈ Integrated safety with safety sensors to protect the operator. βοΈ Flexibility in using packaging rolls according to customer needs. βοΈ High-quality European components to ensure machine durability. Features of the weight packaging machine: βοΈ High speed and high accuracy in packaging. βοΈ Advanced PLC electronic control system enables smooth and responsive operation. βοΈ Durable 304 stainless steel construction materials to ensure hygiene and product safety. βοΈ Practical and easy-to-maintain design to extend the machine's lifespan. βοΈ Integrated safety systems to ensure operator safety. π‘ The ideal solution for filling and packaging food products with utmost efficiency and precision!
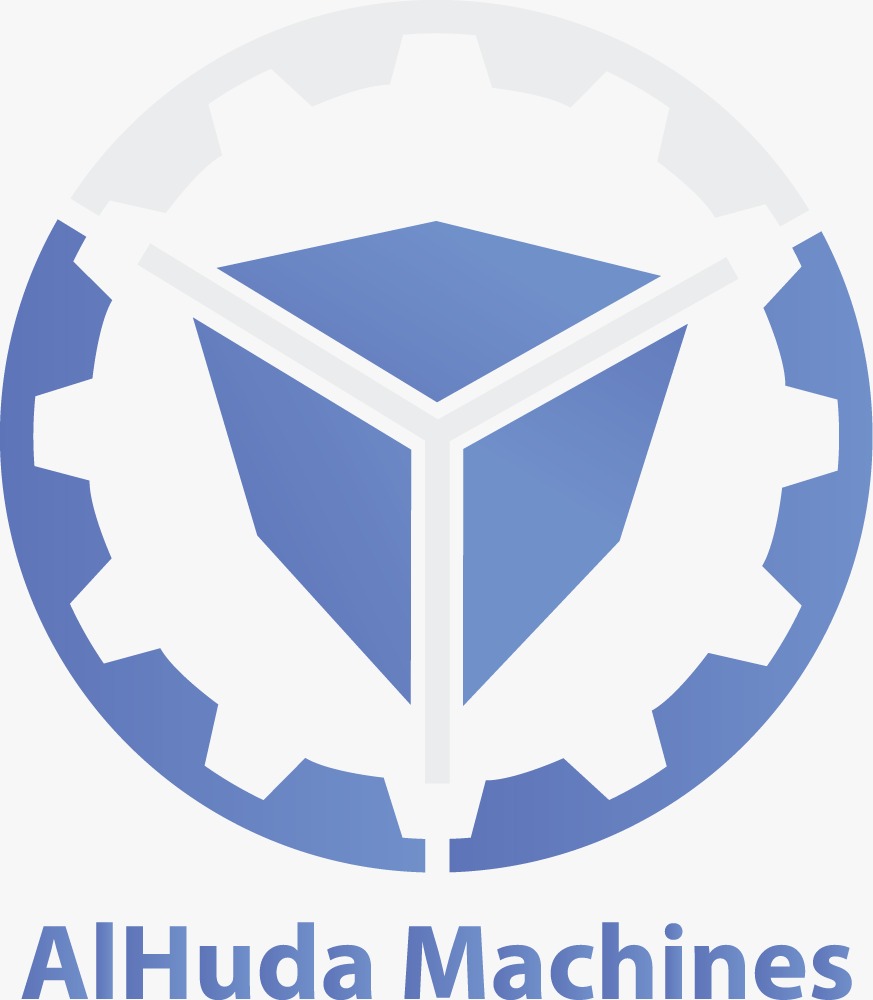
control Board
Schneider brand cutters Schneider brand contactors delta control screen delta inverters Engines company GAMAK YILMAZ gearboxes Or according to the customer's request
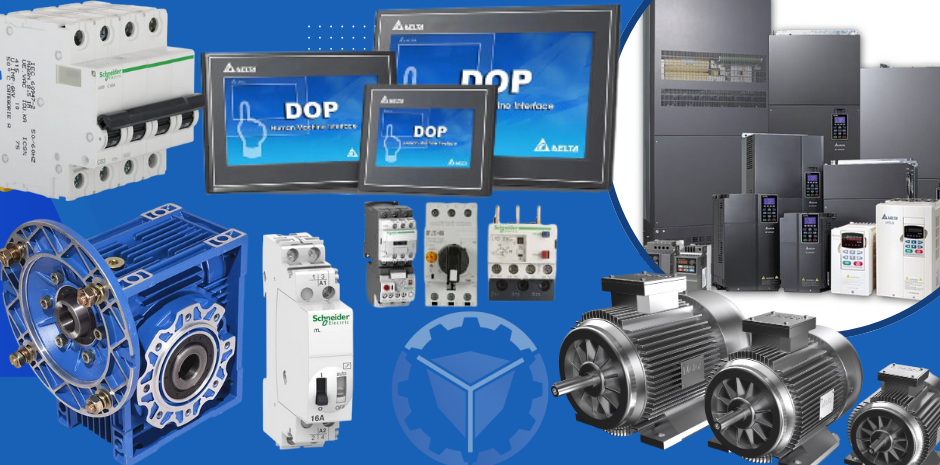
basic information
π½β¨ Corn Chips Production Line β The Smart Solution for Unparalleled Quality Crisps In the competitive world of food industries, Al-Huda International Company stands out with its corn chips production line as a smart, technologically advanced investment option that suits your ambitions and achieves guaranteed profits in the chips and crisps markets. π Manufacturing Efficiency... and Creative Taste This line is specifically designed to convert corn flour into crunchy, delicious, and healthy chips, using modern technologies including mixing, extrusion, shaping, drying, seasoning, and finally packaging. βοΈ Main Line Components β European technology and impeccable precision: 1οΈβ£ Raw Material Mixing Unit πΉ Precisely mixes corn flour with water and additional ingredients to produce a homogeneous dough. 2οΈβ£ Extruder πΉ Operates with heat and high pressure to form the dough into attractive and varied shapes according to the customer's desires. 3οΈβ£ Shaping and Cutting Device πΉ Precisely cuts the product to the desired size and shape before drying. 4οΈβ£ Hot Air Dryer πΉ Removes excess moisture and ensures a balanced crispiness in the final product. 5οΈβ£ Hot Air Oven πΉ For healthy, oil-free roasting β ideal results with a lower-fat, longer-lasting product. 6οΈβ£ Seasoning and Flavoring Unit πΉ Adds the desired flavors with even distribution and an irresistible taste. 7οΈβ£ Packaging Machine πΉ Automatic, airtight packaging maintains product quality and freshness for a longer period. π Features of Al Huda Corn Chips Production Line: β High productivity β Fully automated design ensures continuity and efficiency. β Great flexibility β Produces more than 30 different shapes of corn chips and snacks. β Quality control of taste and texture β Each piece produces the same quality and balance. β Energy and oil efficiency β Economical and environmentally friendly performance. β Simple operation and hygienic construction β Made entirely of 304 food-grade stainless steel according to international standards. π Dimensions and Required Space: πΉ Complete line length: approximately 27 meters πΉ Required width: approximately 3 meters πΉ Required space: approximately 300 square meters π‘οΈ Trust Guarantee β Full Test Before Purchase At Al-Huda, we don't just sell a machine... we offer you a partner in success. π§ The entire line is tested at our factory in Gaziantep, Turkey, in the presence of the customer, to ensure full compliance with the agreed-upon specifications. π In the event of dissatisfaction, the customer has the right to a refund without obligation. π Why Al-Huda? π Over 20 years of engineering experience and professionalism in the food machinery industry. π Production lines that have ISO and CE international quality certifications. β Continuous technical support β before and after the sale. β The ability to customize the line according to the product type and target market. β Fast shipping, full training, and operation in the customer's country. π© We are waiting for your message now! We will provide you with a detailed catalog, high-resolution photos and videos, and a personalized price quote. π Al-Huda Company - Your partner in success, a builder of trust with quality standards and craftsmanship. We don't just offer a production line... We offer you a real project that will change your future. π οΈ Al-Huda International - Where success begins, and crisps are made with excellence.
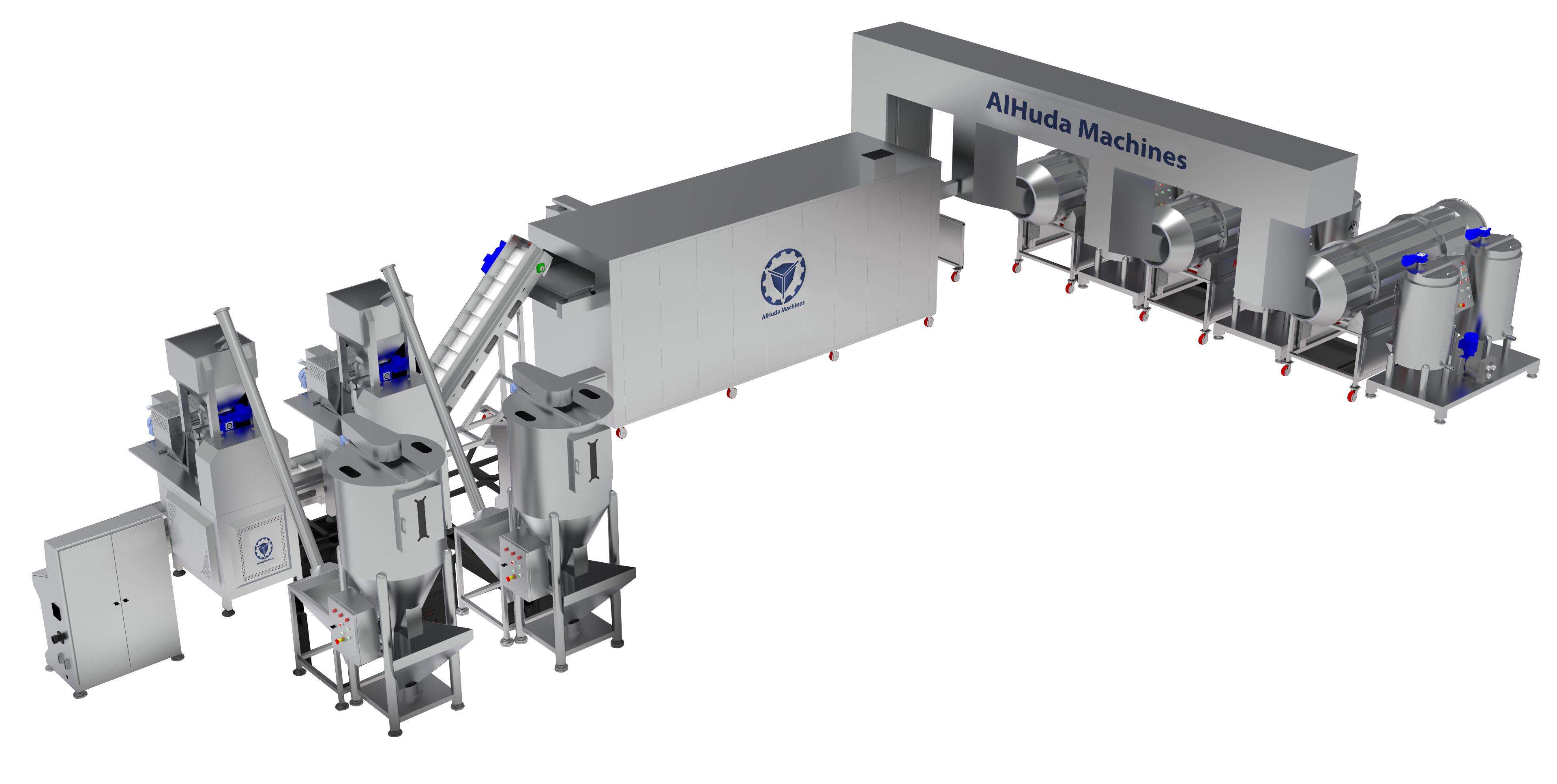
Gallery
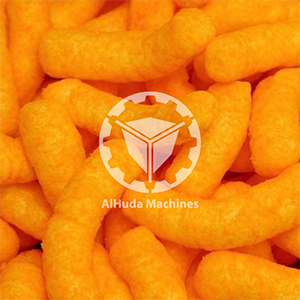
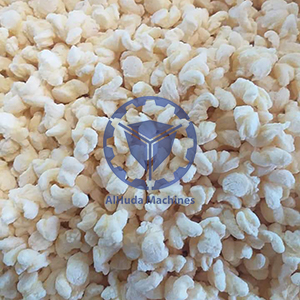
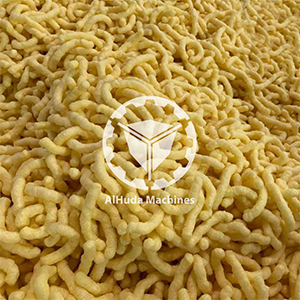
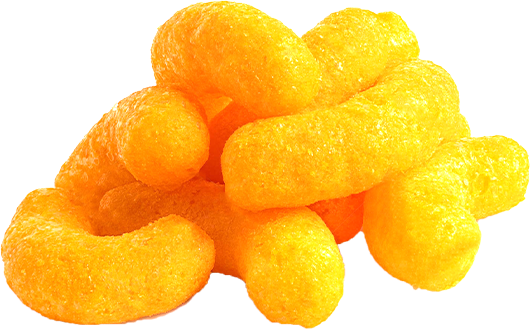
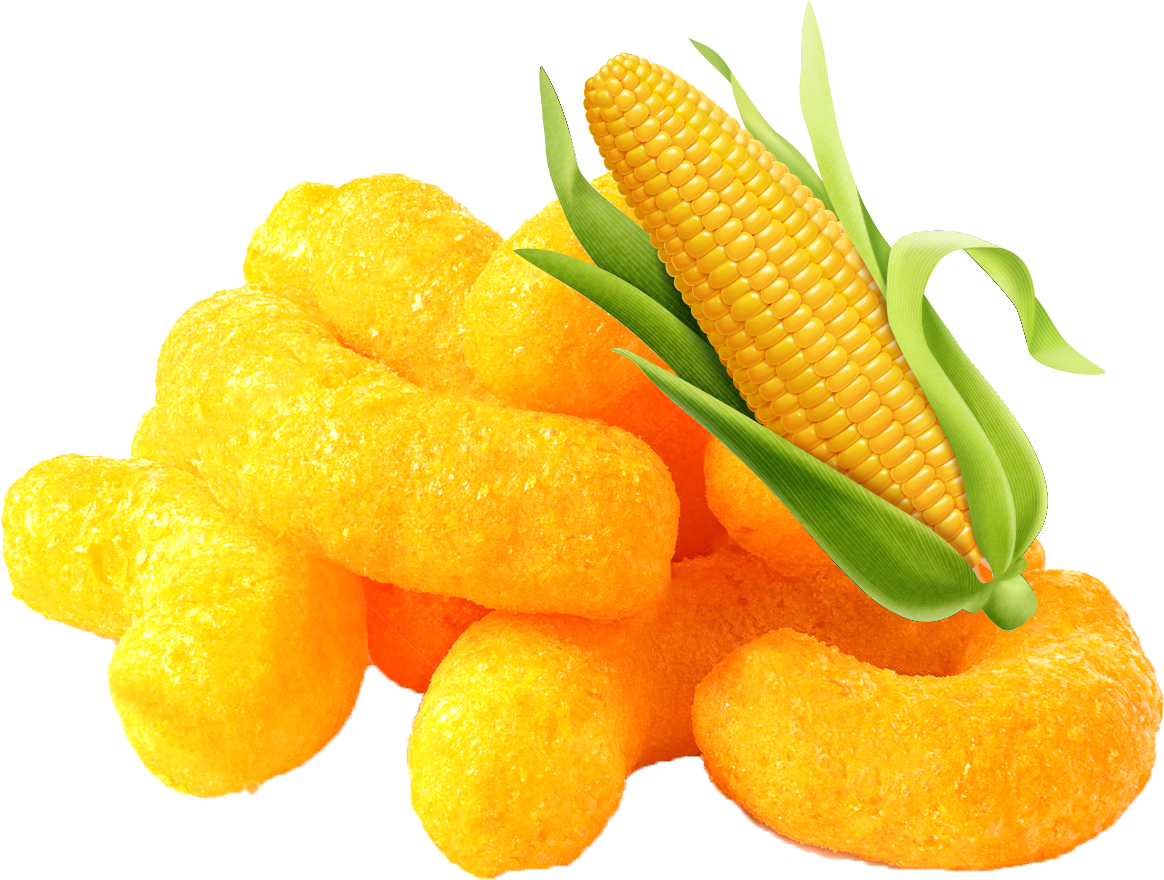